We're Sorry...
The web page you are attempting to view is no longer available.
It could be that the web page name has been changed, renamed or completely removed. Our website is continually under development, and it could quite simply be that the content in question is no longer relevant or out of date.
Use the Search Bar
An excellent way to locate content on our website is by using the search bar at the top of every web page. Our site search engine is powerful and will make suggestions based on the topics you enter. The search function starts suggesting content as soon as you type something.
Please click on the button below to continue browsing..
Return to our Home Page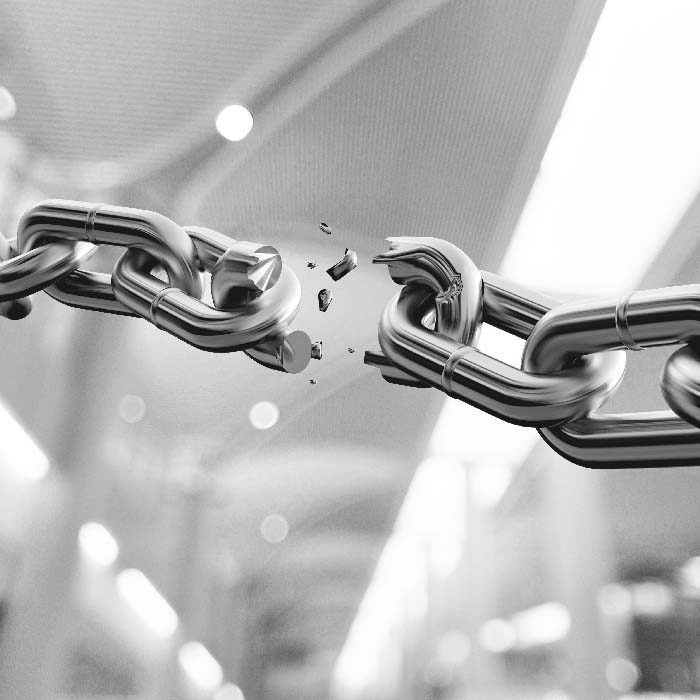